Fuel consumption is a critical concern in the rail industry, accounting for a substantial portion of operational costs. Locomotives have a significant appetite for fuel, with consumption rates ranging from 4-5 gallons per hour while idling to nearly 200 gallons per hour for larger locomotive engine sizes at higher-notch settings. A rough diesel price of $4 per gallon can cost a locomotive over $800 in fuel per hour of operation.
Across a fleet of hundreds or thousands of locomotives, this could mean billions of dollars in fuel used annually which means making even minor efficiency improvements can significantly impact the overall profitability of a railway and its ability to reach its sustainability targets.
Supercapacitor starting assist technologies like KickStart have become complementary to Automatic-Engine-Start-Stop (AESS) systems to reduce engine idle time. As battery levels drop or power availability is required, the automatic-engine-start-stop (AESS) system seamlessly restarts the locomotive engine to provide power or charge the batteries. Since a locomotive may be idling solely to recharge the batteries, an opportunity exists to reduce this time. Battery-related issues contribute to 20% of locomotive engine idling, with 50% of those issues stemming from weakened batteries.
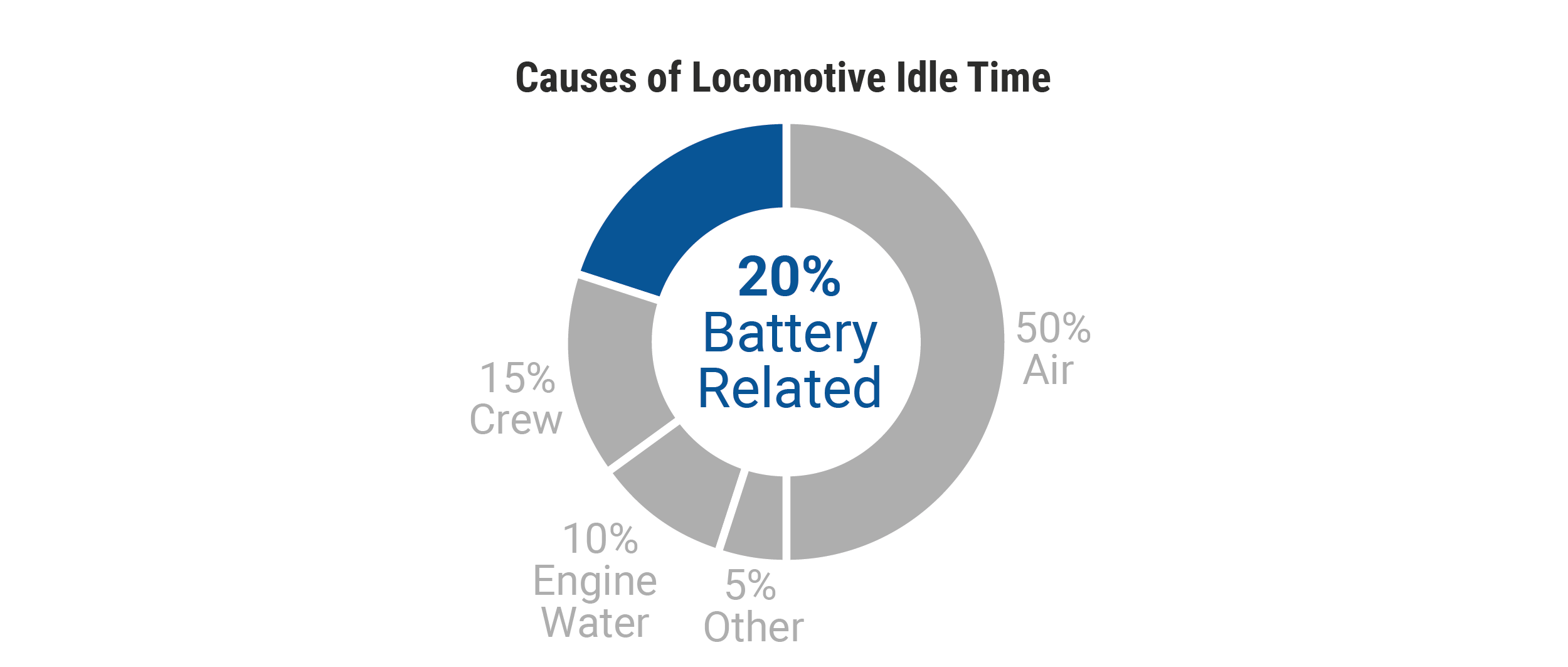
KickStart supercapacitor starting assist offloads the batteries during the entire crank cycle, reducing battery charge time when the engine is running. As a result, the onboard AESS can often shut the engine down sooner with less idle time for battery charging, leading to less fuel consumption and lower emissions. One example shows installing KickStart supercapacitor systems on SD40-2 locomotives resulting in a remarkable 50% reduction in idle time caused by battery charging requirements, going from 36 to 18 hours per locomotive per month. This equated to an additional 18 hours of shutdown per month per unit, significantly decreasing overall idle time.
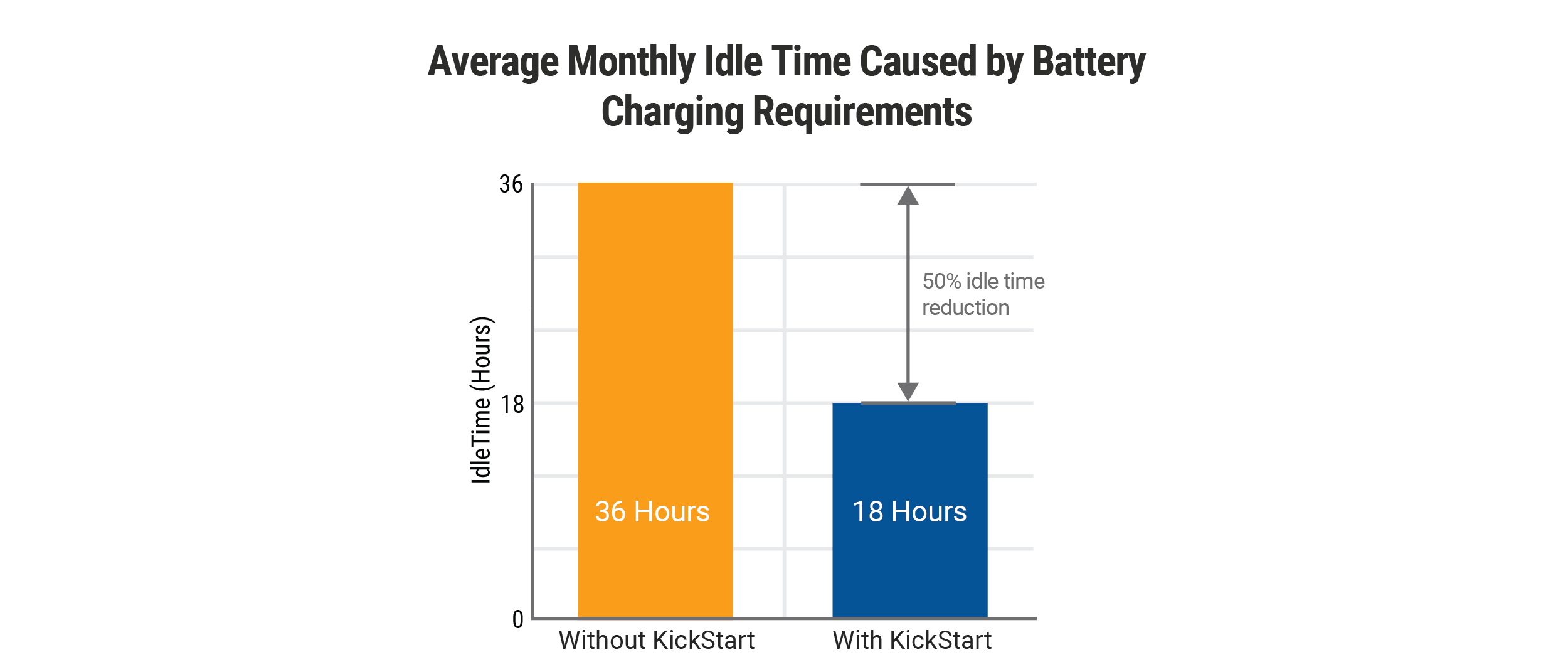
A second study examining overall fuel reductions showed that KickStart provided a 10% reduction in overall idle time by cutting the idle time needed for battery charging. This reduced fuel consumption by over 1,080 gallons per year per locomotive. This equates to roughly $4,320 in fuel alone per locomotive per year. This amount doesn't consider the savings achieved by reducing dead-won't-starts and improving battery longevity.
With fuel savings of nearly $4,500, the potential cost savings are considerable for railway companies with large fleets of locomotives. Adopting supercapacitor starting assist technologies offers a tangible solution for reducing fuel consumption across the entire fleet, improving financial performance and resource management.